Work orders are essential elements for maintenance because they provide relevant details about upkeep, repair, or operations work, such as replacing parts, performing an inspection or returning an asset to operating condition.
What is a work order?
It is a written means of communicating information about a task. For example, an electrician may receive a work order to complete a project at a construction site or to repair installation parts. A maintenance work order provides details about repair or operations such as replacing a part, returning an asset to operating condition, or performing an inspection. A work order is a communication tool that should include all the necessary information to perform a task and specify which team member should carry out particular jobs.
The work order process
A work order process is a system for ensuring accountability and delivery for every step required to complete a work request. A well-defined work order process will reduce equipment downtime and help keep good communication from start to finish. Every maintenance work order has a lifecycle with few main phases that can be broken down into several steps that we have listed here.
Identification
The first step is to identify the issue and report it, mentioning the location. Someone has to create a request. Your company should evaluate this criticality. In this phase, the worker assigned should reported the malfunction. If the cause is unclear, your technicians should add it later.
Creation of a request
The request must describe what is to be done with which resources, to which asset, when, why, and how. All the details of the job should be submitted to the maintenance team for further action.
Prioritization & schedule
After the request is accepted, the supervisor should prioritize the task and schedule it accordingly. It is advisable to set a deadline to keep everyone accountable and informed. Your technicians should know what they are in for and what work orders are most urgent.
The work is assigned and completed
The task will be assigned to a specific technician or team, who will undertake it during the scheduled time.
Closed & documented
After the maintenance task has been performed, it should be marked as complete and documented, so you and your team can keep track of important data for further processes.
What information should a maintenance work order include?
To make a perfect work order, you should include at least the following information:
– A detailed work order should include which parts and tools are required to perform the task.
-Health and safety notes because technicians have to be warned if there are any risks associated with the tasks.
-Expected completion date, expected hours of work, when the order was requested and when it was performed
How to make the perfect work order?
Detailed maintenance work orders should contain a lot of information to help managers, supervisors and workers to organize and assign tasks. In other words, a work order is very similar to a briefing you pass on to your team. However, writing a detailed maintenance work order is not enough; you need to follow the process in order to achieve optimal results.
Digitize your work orders
By doing that, you will reduce the chance of losing them. Your team can keep the work orders on their smartphone at all times, making sending and receiving them easier than ever. Additionally, you do not need to worry about misinterpreting messy handwriting. A digital work order will be available at any time with a clear and unmistakable message.
By digitizing your work orders, it is easier to keep a record system where you could check the asset’s work order history and see the parts that have been recently replaced. Consequently, you could become aware of which replacements have been part of a bigger maintenance issue.
Track your inventory
A work order can help you track time and costs. It can also help you track parts, materials, purchase orders, and receipts. By using an inventory management software you could monitor the quantity, costs, and the details of your inventory in one place. You can even adjust your settings to receive notifications when your inventory is low.
Check what your techs are doing
It is hard to create a work order schedule if you don’t have any insight into what your workers are doing. A Computerized Maintenance Management System CMMS will show you which workers are assigned to which tasks in real time so you can keep an eye on all the tasks, manage approvals, and send invoices. Monitoring your technicians’ duties is important to ensure that nobody is overloaded with jobs, situation that could slow turnaround time for work orders.
Make the difference between reactive and preventative maintenance
Reactive maintenance refers to repairs parts when equipment has already broken down, in order to restore it. In this case, operations must cease until the piece of equipment is repaired. On the other hand, preventative maintenance includes checking equipment rand replacing small parts to prevent unexpected break downs.
Implement a preventive maintenance plan
By performing a regular preventive maintenance, you will make sure your equipment remains in good conditions, both for the machine and the operators. A can preventive maintenance plan can help you to save resources and make all process more efficient. Preventative maintenance procedures take less time than emergency repairs and replacements. If your business has been relying on reactive maintenance for your equipment, you should consider switching to a preventive maintenance strategy.
Use mobile devices to manage work orders
Mobile devices are a great tool for work orders maintenance management. By using a work order app, you can send orders on the go shortening response time. You can create, modify or update a work order directly from their phones or tablets. If you have a mobile bar code scanning, there is not need to search equipment manufacturer databases with key words and filters for manuals. Instead, work orders can be created when a bar code is scanned with a smart phone or tablet.
Select the correct assignee
Choosing the right assignee is an essential part of the work order process. Failure to choose the right technician might cause delays or it may lead to even bigger problems than the original one. Before selecting the assignee, there are many important questions that you should ask such as “How many people does the task require?” or “Why should I choose this particular technician?”
Another significant thing to consider in choosing the correct assignee is whether you require an outside contractor or not. If the task is too much for your team, you need to find another way to handle the issue. In such moments, an outside contractor to assign the task might be right answer.
Check your data
By monitoring your preventive and corrective maintenance work orders with the collected data, you could preventive maintenance plans that will help you to save time and money by reducing failures and mean time to repair (MTTR). Sure, you might need to process quite a lot of data, but the secret for managing your work orders more efficiently is in the details.
How can you manage maintenance work orders more efficiently?
Always keep in mind what we said at the beginning of this article: work orders are primarily communication tools. Making a perfect work order is all about passing on the right information through all the stages of the process.
So, how can you organize better maintenance work orders? Pen and paper are definitely out. Besides being an environment unfriendly option, it is nor the most efficient alternative for the time being. During years, Excel sheets were great for maintenance planning. They were cheap, harder to lose and easy to archive. However, today, businesses need a more effective powerful and cutting-edge technology. Then maintenance software comes along. By using Computerized Maintenance Management System (CMMS), you can store every work order in the cloud, which makes it available to all of your team at all times. A mobile device is enough to keep them up to date with notifications and requests. It also become easier for your clients to make a work request.
Work order software expands the capabilities of manually generated work orders in many ways. Firstly, it allows you to attach photos of the asset and the repair needed order. Secondly, you can send the precise location of an asset within a facility. Thirdly, the mobile work order component makes it possible to access an asset’s prior maintenance history, providing technicians valuable information about the best way to approach a task. Finally, work order tracking is simpler than ever using the CMMS mobile device capabilities.
This is how it all should work, at least in theory. Conclusively, regardless of your preferred method for organizing and managing work orders, everything comes down to how people use and communicate relevant information. A CMMS relies on the data you provide it. If you and your team make good use of your CMMS, inserting all the necessary data to perform tasks and collect reliable data, it will work nicely and efficiently. If not, it will be just as unreliable as any other method. To avoid this, we strongly suggest that you request help to train your employees during the onboarding phase.
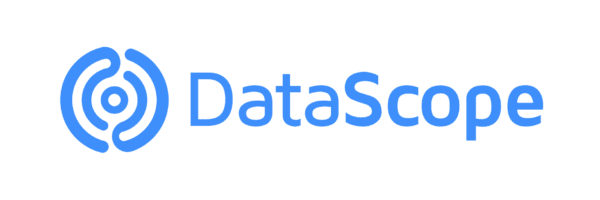
DataScope is a platform which allows various industries to streamline, organize and evaluate the work of their field staffs thanks to online forms which provide real time indicators 100% adaptable to any field.