El cuidado de los activos es fundamental para la operatividad y eficiencia productiva de las empresas. Para cumplir dicho objetivo, hay que diseñar e implementar una estrategia de mantenimiento correctivo, preventivo o predictivo para evitar fallas, accidentes y detenciones provocadas por el desgaste natural de piezas, equipos y maquinarias.
La base esencial para el éxito de este planeamiento estratégico radica en contar con un adecuado programa de mantenimiento. Una de las bases esenciales para el éxito de una compañía, radica en contar con un adecuado programa de mantenimiento.
Solo de esta manera se optimizará la seguridad de las operaciones y la continuidad del servicio. Además, se reducirán al mínimo los períodos de inactividad y se incrementará la eficiencia de toda la organización.
¿Por qué el mantenimiento es tan importante para el éxito de una empresa?
Ninguna máquina, herramienta o equipo puede funcionar correctamente si no recibe mantenimiento. Es una condición esencial e ineludible, sin importar sus características, modernidad, diseño o tecnología.
Esto se debe a que la operación constante de partes, piezas y componentes, sean mecánicos o electrónicos, se traduce en desgaste, el que a su vez genera la respectiva probabilidad de fallas.
Esta situación es más evidente en el caso de activos industriales que operan durante extensas jornadas. Por ejemplo, hornos, cintas transportadoras, empacadoras, grúas, tornos, aires acondicionados, perforadoras y cosechadoras, entre otros equipos críticos para las empresas.
Para enfrentar esta situación las empresas deben diseñar e implementar un plan de mantenimiento que regule, monitoree y optimice el rendimiento de sus activos.
Todo ello con el objetivo de verificar sus condiciones de funcionamiento y, en lo posible, extender al máximo su eficiencia y vida útil.
Para alcanzar esta meta, el mantenimiento debe realizarse de acuerdo con una pauta metodológica precisa y coherente. Así se garantizará mayor duración y mejor rendimiento de las maquinarias, equipos o instalaciones.
Con ello se elimina el daño que provocan los extensos periodos sin producción derivados de una falla inesperada. Contingencias que siempre se traducen en considerables pérdidas de recursos, horas de trabajo, ingresos y utilidades.
Al mismo tiempo, se amortizan los costos operativos de la empresa, tanto en el corto como en el largo plazo.
¿Cuáles son los principales tipos de mantenimiento?
Definir e implementar un modelo de mantenimiento para maquinarias y equipos, tiene diferentes finalidades y objetivos:
- Mantener la fiabilidad de sus activos para que funcionen de manera continua y eficiente.
- Prevenir roturas o fallas, maximizando la vida útil del equipo.
- Minimizar las pérdidas de producción y cumplir los plazos de entrega a clientes.
- Mantener la seguridad y salud de la fuerza laboral.
- Reducir costos y riesgos en general.
Sin embargo, los planes de mantenimiento también pueden ser de diverso tipo, de acuerdo con las características, necesidades y objetivos estratégicos de cada empresa.
Los expertos definen tres tipos principales de mantenimiento:
- Correctivo
- Preventivo
- Predictivo
Si bien cada uno de ellos tiene características y ventajas propias bien definidas, algunas empresas pueden requerir un programa de mantenimiento que combine los tres tipos.
La combinación más adecuada se determina considerando las siguientes variables:
- Pérdidas potenciales derivadas de las detenciones de producción para cada equipo específico.
- Costo de mantenimiento vs. costo de reparación del equipo.
- Impacto ambiental de las acciones adoptadas.
- Seguridad y salud en el trabajo.
- Efectos finales en la calidad del producto o servicio entregado.
Del mismo modo, hay que analizar los objetivos estratégicos de la empresa, incorporando los respectivos análisis de costos de las tareas de mantenimiento y de las eventuales fallas, así como también, de los riesgos potenciales que cada dirección ejecutiva esté dispuesta a aceptar.
A su vez, es importante contar con el apoyo de especialistas en ingeniería de mantenimiento. Ello permitirá establecer un plan consistente con las actividades de la empresa, su posicionamiento estratégico y las características de sus respectivos activos.
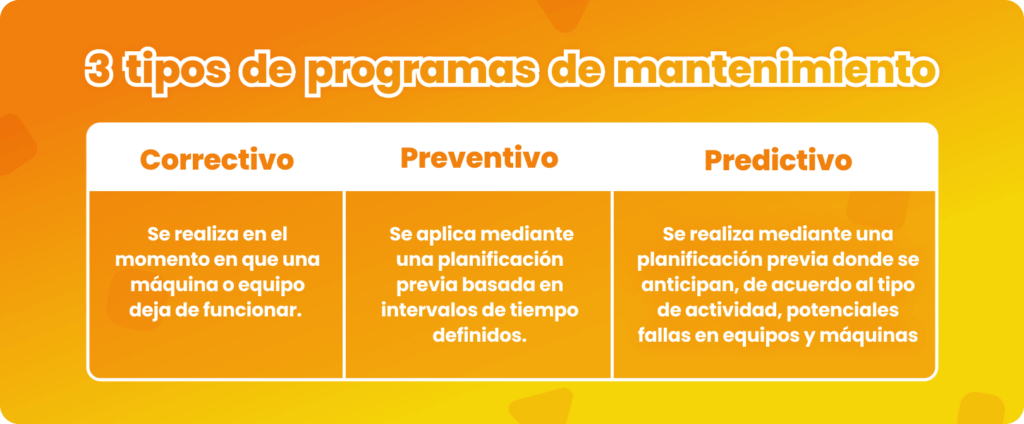
¿Qué es el mantenimiento correctivo?
El mantenimiento correctivo, también conocido como “mantenimiento de descanso”, es el que se realiza a todas las máquinas o equipos que dejan de funcionar. Implica reparar fallas o desperfectos de diversa índole. Por lo tanto, es un mantenimiento reactivo.
En este escenario, la maquinaria o equipo falla inesperadamente o bien sufre un nivel de desgaste tan alto, que necesita una intervención de emergencia para que cumpla o reanude satisfactoriamente su función productiva.
El mantenimiento correctivo se aplica cuando los encargados de área estiman que el tiempo de inactividad y los costos de reparación de las máquinas o equipos que fallan, serán menores que la inversión requerida para aplicar una estrategia de mantenimiento programado.
Esta estrategia puede ser rentable para empresas pequeñas, o que operan con bajos volúmenes de producción.
Sin embargo, pierde validez cuando ocurre una falla catastrófica que paraliza toda la faena o servicio.
¿Qué es el mantenimiento preventivo?
El mantenimiento preventivo, en cambio, se aplica mediante una planificación previa basada en intervalos de tiempo definidos de acuerdo con un criterio preestablecido.
Dicho criterio puede basarse en diversas variables tales como:
- Características de maquinarias y equipos.
- Intensidad y complejidad de los procesos productivos.
- Duración de las faenas en la empresa.
- Nivel de desgaste del equipo.
- Recomendaciones generales del fabricante
El objetivo del mantenimiento preventivo, también conocido como “Mantenimiento Basado en el Tiempo” (MBT), es reducir el riesgo de fallas o eventuales pérdidas en el rendimiento de la maquinaria, así como prevenir accidentes y detención de tareas.
Es muy eficaz para evitar fallas relacionadas con el desgaste o envejecimiento de equipos y maquinarias. Por ende, es la estrategia más extendida y utilizada en las empresas modernas.
Principales ventajas del mantenimiento preventivo:
- Reduce las fallas de las maquinarias y las detenciones del proceso de producción.
- Incrementa la vida útil de los activos y de las plantas industriales.
- Optimiza el ahorro de materiales, repuestos y tiempo de trabajo.
- Reduce el consumo de energía gracias al funcionamiento eficiente de máquinas y equipos.
- Genera menos interrupciones en el conjunto de tareas diarias.
- Brinda mayor seguridad a los trabajadores.
Principales desventajas del mantenimiento preventivo:
Pese a estos importantes beneficios, el mantenimiento preventivo también tiene algunas desventajas. Estas son las siguientes:
- No elimina por completo el riesgo de averías o paradas inesperadas.
- Es intensivo en el uso de mano de obra.
- Puede dañar piezas críticas de máquinas que aún funcionan correctamente y no necesitan mantenimiento.
- No siempre permite establecer los intervalos de tiempo más apropiados para las tareas de mantenimiento.
- El ahorro obtenido sólo puede medirse a mediano y largo plazo.
¿Qué es el mantenimiento predictivo?
Como su nombre lo indica, el mantenimiento predictivo utiliza técnicas e instrumentos que controlan las condiciones o estado de las máquinas, su rendimiento y los posibles indicadores de fallas.
De este modo, es posible “predecir” el momento exacto en que necesitan una intervención o mantenimiento y así evitar que se produzca una falla.
El objetivo del mantenimiento predictivo es realizar la intervención del equipo en el momento preciso. Ni antes ni después. Consecuentemente, se reducen los costos, se optimiza el uso de recursos y se maximiza el tiempo de producción.
Estas características hacen que el mantenimiento predictivo sea conocido también como “Modelo de Mantenimiento de Alta Disponibilidad”. Este se aplica a equipos esenciales y que bajo ningún concepto pueden fallar ni dañarse.
Es decir, el mantenimiento predictivo se utiliza principalmente en equipos que requieren disponibilidad superior al 90%, y cuya falla puede tener graves consecuencias para la empresa. Por ejemplo, un horno de panadería, una perforadora minera o una aserradora forestal.
Esta alta demanda es, precisamente, el indicador que establece la necesidad de que un equipo sea monitoreado constantemente y que su mantenimiento debe ser predictivo.
El mantenimiento predictivo también permite identificar fallas aleatorias inesperadas, que según las estadísticas representan el 80% de los patrones de falla.
En todos estos casos, el procedimiento estándar corresponde al monitoreo constante de la condición del equipo.
Principales ventajas del mantenimiento predictivo:
- Aumenta la vida útil de los activos y sus componentes.
- Reduce los costos de repuestos y horas de trabajo asociadas a tareas de mantenimiento.
- Mejora la seguridad de los trabajadores y del entorno productivo.
- Maximiza la productividad de los activos.
- Reduce los costos de producción.
Principales desventajas del mantenimiento predictivo:
Aplicar un esquema de mantenimiento predictivo brinda múltiples beneficios, pero también tiene sus desventajas.
Estas son las siguientes:
- Requiere trabajadores calificados y con alta capacidad de realizar análisis de datos.
- Precisa una fuerte inversión en equipo para monitoreo y diagnóstico.
- Requiere un sólido y constante compromiso de gestión de parte de los equipos.
La importancia de la tecnología para el éxito de las tareas de mantenimiento
Este conjunto de características, ventajas y desventajas reafirma la necesidad de que las empresas apliquen un modelo de mantenimiento apropiado a sus características y necesidades específicas.
En DataScope entendemos la importancia estratégica de implementar un programa de mantenimiento efectivo y eficiente. Por ello, ponemos a tu disposición avanzadas soluciones para gestión digital de activos empresariales.
Mediante la aplicación de listas de verificación electrónicas puedes, por ejemplo, implementar procesos de monitoreo continuo que te permitirán verificar el estado de las máquinas y equipamiento crítico de tu empresa.
También podrás elaborar y guardar informes sobre el estado de tus activos, directamente en los dispositivos móviles de los equipos a cargo de la inspección, y complementarlos con imágenes, incluso sin estar conectado a Internet.
De este modo, podrás contar en todo momento con una descripción exacta de las condiciones operativas de cada máquina y almacenar datos valiosos que luego pueden exportarse y analizarse en forma ágil y oportuna.
Característica que se refuerza gracias la integración de DataScope con más de 1.500 otras aplicaciones de uso intensivo.