There is no better way to ensure a program’s success than a boots-on-the-ground, face-to-face site inspection. Stepping away from the office to visit a location is essential to make relevant and well-informed decisions.
What are site inspections?
Site inspections are a set of activities implemented to check and verify the on-field compliance including safety standards, quality assurance, working conditions, and other critical areas of work site. On-site inspections allows us to have a broader view of the business operations, enhance the attendee experience, help you to plan the logistics and to experience the level of service your attendees can expect.
Why you should conduct site inspections?
Conducting site inspections can bring many benefits to your business. Here we have listed some of them:
To meet the people you work with
Build relationships with tour team is essential to build trust and confidence, and to achieve success.
Detailed inspections of the quality of installations
By doing that you can check if the installations comply to standards and specifications.
To check factory compliance and quality monitoring systems
These factors are foundational to achieving compliance and quality monitoring objectives
To eliminate and minimize risks
It is important to consider all foreseeable hazards and details to lessen the potential damage that can be caused by a hazard or danger. Your company need to have a risk assessment form available to be used when an accident occurs.
Measuring onsite inspection effectiveness: What are KPIs?
Key performance indicators (KPIs) are used in businesses to measure progress toward specific goals or simply to monitor trends associated with corporate activities. KPIs are structured data, which can be used to show us how far are we from our goals and where further improvements and resources are required.
How do we select KPIs?
The best KPI selection for a particular organization depends on several factors such as: What do you want to achieve with on-site inspections? Where does the organization want to be tomorrow?
To develop meaningful KPIs, managers need to understand their operations, evaluate the systems that are in place to manage risks, and understand the company’s business plan and culture. You should be clear about where would you like the organization to be in the short and long term. Once processes and goals have been evaluated, KPIs can be selected.
The purpose of store inspections is to control and analyze production, distribution and commercialization processes and identify any anomaly that may result in risky situations for workers, customers and for the organization in general.
Other objectives of field inspections are:
- Evaluate business administration and management.
- Identify unforeseen issues in the workplace.
- Diagnose deficiencies within the work team.
- Analyze accounting and internal control systems.
- Detect any problem that may arise.
- Identify undesired effects of changes introduced in the production process or in the administrative management.
- Propose solutions to problems or deficiencies found.
Managing KPIs for field inspections
For business owners is a priority to create a unified ecosystem that learns how to improve and strengthen trust continuously. t without tight integration across a production network, quality goals will never be met and compliance shortfalls will happen. For brands and retailers is essential to create Corrective Action Preventative Action (CAPA) in order to build a reputation and consistently deliver flawless production. Brands and retailers holding suppliers should create a cycle of continuous improvement where returns and complaints from customers, process variations and production inconsistencies need to be managed using the CAPA process.
For KPIs to be successful, you need to implement a system for tracking, communicating, and improving performance. Bear in mind that KPIs might evolve as the organization changes. You and your team should be prepared to continuously evaluate the progress in tracking performance and the benefits of the KPIs. When necessary and appropriate, KPIs should be modified to reflect changing circumstances or drive further improvement.
Here we have selected a list of KPIs relevant for on-site inspections.
Corrective Action/Preventative Action (CAPA) events
Also known as Corrective Action Requests (CAR), CAPAs are used for eliminating anomalies and non-conformances in products that are often discovered during inspections. When a product inspector finds a variation in product quality and sees patterns of non-conformance, they create a CAPA. Tracking CAPAs and their trends are paramount for troubleshooting problems across production networks as well.
Perfect Order Index (POI)
It is a metric of how exactly a company fulfills a customer’s order since taking the order correctly, allocating inventory immediately, delivering the product on time and sending an accurate invoice.
The formula to calculate the perfect order performance is:
(Percent of orders delivered on time) * (Percent of orders complete) * (Percent of orders damage free) * (Percent of orders with accurate documentation) * 100.
Manufacturing Cycle Time
This metric quantify the amount of elapsed time from when an order is taken until the product is produced and entered into finished goods inventory. Cycle times vary by industry, size, scale of factory operations, locations and relative stability of supply chains. This is an essential metric for any brand or retailer to manage their factory operations, as it shows how well forecasting, manufacturing planning, sales, marketing, and distribution are orchestrated with each other.
Number of audits or inspections performed
The goal of an audit is to assess overall compliance with one or more regulations, internal policies, or other compliance drivers. Audits are typically conducted by a third-party to the site being audited, which could include an auditor from a corporate department or an auditor completely external to the company. An inspection is typically something that a site is required to do by a compliance obligation.
Number of reported accidents & incidents
This metric gives a high-level benchmark to the organization in terms of showing if safety is improving or worsening. In addition to monitoring the number of accidents/incidents, you should convert this number to a ratio per employee. It is advisable to keep a close eye on this KPI during times of change (new products, new processes, new machines, etc.). In this item, you should include all workplace illnesses, injuries, near misses and accidents. no matter how minor an injury is. If the amount of incidents is increasing, it is necessary to take further measures.
Total recordable incident rate
Total Recordable Incident Rate (TRIR) or Total Case Incident Rate gives the company a look at the organization’s past safety performance by calculating the number of recordable incidents per 100 full-time workers during a one-year period. The lower the TRIR, the better a company’s performance is. Organizations can benefit from tracking this metric year-by-year to improve their standards. TRIR gives you insight into your company’s past safety performance. Incident rates are an indication of how many incidents have occurred within a timeframe. If this rate is high, this indicator show as that there is something wrong with the safety system.
Near miss incidents
A near miss is an unplanned event that did not result in injury, illness, or damage – but had the potential to do so. If the number of near miss incidents are growing, the cases should be analyzed in other to prevent injuries or damage. Recognizing and reporting near miss incidents can significantly improve worker safety and enhance an organization’s safety culture.
Lost time injury incidence rate
This measures the events that occur over a timeframe by a standard number of people. So if you want to calculate the ‘LTIIR’ (Lost Time Injury Incidence Rate) for 1,000 people, you multiply the number of incidents by 100, then divide it by ne number of people. So, if you have 3 incidents, multiply that number for 100. The result is 300. The divide that by the number of people and we get a LTIIR of 0.3.
Lost time injury frequency rate
This refers to the number of lost time injuries that happen per million hours worked. So a ‘LTIFR’ of 8, means that 8 lost time injuries take place every million hours worked. To work out the LTIFR you multiply the number of lost time injuries by 1,000,000 then divide that number by the total number of hours worked in an organization. For instance, if you have 8 lost time injuries and 3 million hours worked, your LTIFR is 2.6.
Equipment breakdowns
Often when critical equipment breaks down, there is a loss of activity. Therefore, this is a strong lead indicator that will play a huge role in the reduction of incidents, since a large percentage of incidents happen due to the state of the equipment used. By measuring the number of equipment breakdown and trying to improve this number, you will affect positively both safety and production.
Employee perception of management commitment
This KPI could be measured through regular surveys. These allow an organization to understand what employees feel think about their jobs and manager and to check if their objectives are on the same path.
Average overtime hours per person
This average is a great KPI to help measure the average time worked by someone beyond their normal working hours. The idea is that if you keep this number low, it can mean that an organization is successfully managing workload and reducing the chance of fatigue in the workplace. You do want to be careful with this KPI, as it is not applicable to all types of organizations and the definition of ‘overtime’ will vary per organization.
Employee satisfaction index (ESI)
This index measures feedback on how satisfied employees are with their jobs and companies. The ESI is a number between 1 and 100 that you should measure over time. You can obtain this metric deploying an employee surveys to get relevant information from your team.
These metrics provide insights into the areas where a company is excelling and where there is room for improvements. Combining and analyzing the data provide by these metrics you can predict future quality outcomes and also troubleshoot potential product quality issues in the future.
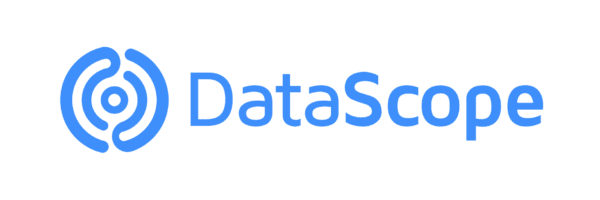
DataScope is a platform which allows various industries to streamline, organize and evaluate the work of their field staffs thanks to online forms which provide real time indicators 100% adaptable to any field,.
Image credits: Pixabay