El método AMEF es una herramienta de análisis que permite detectar las causas y efectos de todas las contingencias que afectan la continuidad operativa de las actividades productivas e industriales. Se trata de una metodología que ayuda a optimizar la competitividad de las empresas y, al mismo tiempo, incrementar la seguridad de los trabajadores.
¿Qué es el método AMEF?
Uno de las metodologías más exitosas y utilizadas en la actualidad para analizar las causas de incidentes y prevenir su reiteración, es el “Análisis del Modo y Efecto de Fallas”, también conocido como método AMEF.
Esta herramienta fue diseñada específicamente para identificar fallas en productos, procesos y sistemas. Todo ello permite evaluar y clasificar de manera objetiva sus causas, características y efectos, mediante un procedimiento analítico y estandarizado.
Los principales objetivos del método AMEF son los siguientes:
- Reconocer y evaluar las distintas fallas que pueden producirse en máquinas, instalaciones o procedimientos, y determinar sus causas basales.
- Determinar los efectos que puedan tener esas potenciales fallas.
- Identificar la forma de suprimir o disminuir la probabilidad de que ocurran nuevas fallas.
- Documentar todo el proceso para generar bibliografía de apoyo.
¿Cuáles son los principales tipos de análisis AMEF?
El método AMEF puede adaptarse a las necesidades y características de toda empresa, sin importar su tamaño, características o segmento de mercado donde participe.
Esto se traduce en la posibilidad de aplicarlo libre y eficientemente a cualquier sector, producto, proceso o sistema de trabajo.
Esto se refleja, por ejemplo, en las siguientes posibilidades de aplicación:
Productos
Cuando se aplica a productos específicos, este método, actúa como herramienta predictiva para detectar posibles fallas de diseño y desarrollo.
Procesos
En los casos que es aplicado a procesos, sirve como herramienta para detectar posibles fallas en las distintas etapas de producción.
Sistemas
Cuando se aplica esta metodología a sistemas es posible detectar, por ejemplo, posibles errores en el diseño de softwares y aplicaciones móviles.
Cada uno de estos usos aumenta, en sus respectivos campos de aplicación, las probabilidades de anticipar los efectos de las diferentes contingencias.
¿Qué tipos de análisis AMEF existen?
Una de las grandes fortalezas del método AMEF radica en que puede aplicarse de distintas formas. Esto se traduce en alta flexibilidad para adaptarse a distintos procesos y contextos productivos.
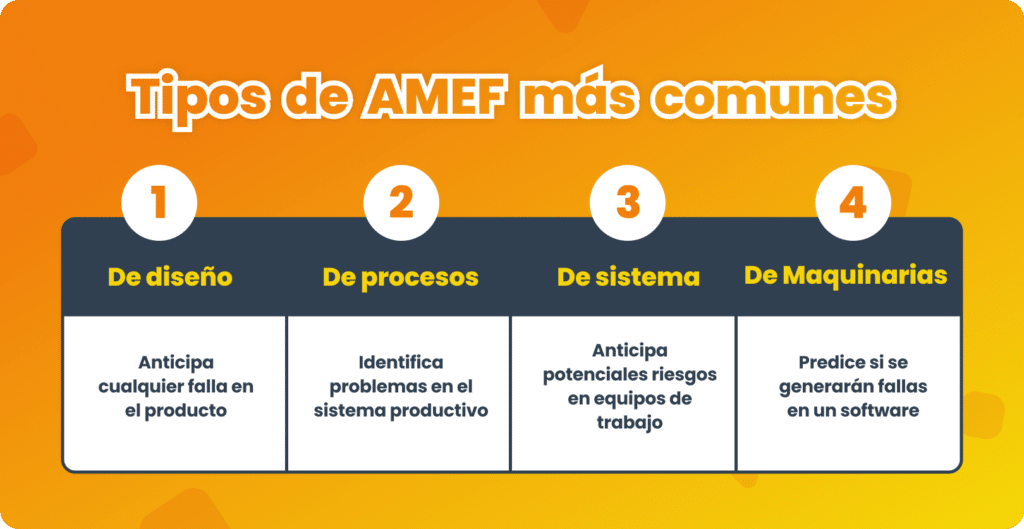
Los especialistas internacionales identifican y clasifican los siguientes tipos principales:
1. AMEF de Diseño
Este tipo de análisis, busca evaluar la conformidad del producto final de acuerdo con las exigencias del cliente. De este modo se puede determinar la calidad final y asegurar el cumplimiento de ciertas especificaciones.
2. AMEF de Proceso:
En este caso se examina cada una de las fases de un proceso, para determinar si las posibles fallas se relacionan con alguno de los componentes del método de las 5M:
- Mano de obra
- Material
- Materias primas
- Método
- Medio ambiente
3. AMEF de Sistema:
Aquí se verifica la compatibilidad entre los componentes de un sistema. Esto permite, por ejemplo, predecir cómo se generarán errores en el diseño de un software.
4. AMEF de maquinarias y/o equipos:
Se utiliza para comprobar y optimizar la fiabilidad de máquinas y equipos. El objetivo es identificar lo antes posible los puntos críticos y analizar las posibles consecuencias en el proceso de producción y en el entorno de trabajo.
5. AMEF funcional:
Se centra en reconocer y analizar las potenciales contingencias operativas de un determinado diseño o concepto.
6. AMEF de Flujo:
Busca identificar fallas y problemas relacionados con la cadena logística y/o de suministro (incluyendo tanto materias primas como información vital para la producción).
A pesar de sus diferencias operativas, todos estos métodos AMEF tienen el mismo objetivo: Recabar información y determinar planes de acción para prevenir contingencias productivas y/o de seguridad.
Estas acciones pueden expresarse en:
- Planes de control de calidad
- Estrategias de salud y seguridad laboral
- Planes de mantenimiento preventivo o predictivo
- Calendarios de visitas inspectivas a terreno
¿Cuáles son las principales ventajas del método AMEF?
Como hemos analizado, este método, es altamente dinámico y permite recopilar información de diferentes procesos, productos y sistemas en general.
En este sentido, algunas de sus principales ventajas son las siguientes:
- Conocer a fondo el producto, el proceso o el sistema utilizado por la empresa.
- Descubrir las debilidades propias y evaluar la gravedad de sus potenciales efectos.
- Establecer niveles de confiabilidad para detectar fallas.
- Evaluar, mediante indicadores específicos y objetivos, la relación existente entre gravedad, ocurrencia y detectabilidad de las fallas.
- Diseñar nuevos procesos, productos y/o servicios.
- Generar y aplicar nuevas estrategias de mantenimiento preventivo y/o predictivo.
- Obtener procesos de desarrollo más cortos y seguros.
- Identificar oportunidades de mejora.
- Obtener más satisfacción de los clientes.
- Generar nuevos conocimientos especializados (know how).
- Transformar la información obtenida durante la aplicación del método, en recursos para capacitar al personal.
¿Cómo implementar correctamente el método AMEF?
Gracias a su dinamismo y flexibilidad, el método AMEF no requiere condiciones específicas para implementarlo en una empresa.
Sólo se necesita un profundo trabajo previo de recolección de información. Esto permite contar con la evidencia documental suficiente de todos los elementos que componen el proceso productivo (herramientas, equipos, infraestructura y talento humano, entre otros).
Desde el punto de vista sistemático, los expertos en seguridad recomiendan aplicar el método AMEF en el siguiente orden:
1. Determinar el objetivo y alcance
Antes que todo debemos tener claridad del proceso, producto o sistema que queremos analizar. Lo ideal es tener a mano toda la información sobre la cadena productiva, las materias primas, el producto final y sus potenciales clientes, entre otras variables importantes.
2. Formar un equipo multidisciplinario
Otro punto importante es crear un equipo de trabajo interdisciplinario para que el análisis sea más enriquecedor. Además, debemos contar con un líder experimentado y que tenga las competencias necesarias para aplicar el método AMEF.
3. Determinar los tipos de fallas
Para realizar esta tarea, necesitamos estudiar toda la documentación reunida durante el proceso de estudio previo. Esta será la base para analizar las posibles fallas que pueden producirse en nuestra empresa, así como su respectiva gravedad y probabilidad de ocurrencia.
4. Identificar causas y efectos de las fallas
El equipo debe determinar las causas y efectos cada falla descubierta. Para identificar las causas, podemos utilizar otras herramientas de análisis complementario, como por ejemplo el Método Espina de Pescado, el Modelo de Frank Bird o el Método de los 5 Por Qué, entre otros.
A su vez, para clasificar los efectos, debemos definir áreas específicas, tales como pérdidas materiales, pérdidas económicas y perjuicios a los trabajadores, entre otras.
5. Evaluar las fallas
En este punto definimos la gravedad potencial de las fallas, de acuerdo con el siguiente criterio:
- Severidad (gravedad de los efectos).
- Frecuencia (diaria, semanal, mensual, bimestral, trimestral, semestral, anual, etc.).
- Detección (remota, media o alta).
Para tales efectos, los expertos sugieren trabajar con una escala tipo de 1 a 10, donde 1 representa el valor menos relevante; y 10, el más alto. De este modo determinaremos el respectivo “Índice de Prioridad de Riesgo” o IRP.
6. Priorizar las fallas
Una vez que calculamos el IRP, debemos clasificar las fallas de acuerdo con su nivel de criticidad para las operaciones de la empresa (bajo, medio o alto). Esto nos permitirá establecer un punto de partida para priorizar las respectivas acciones correctivas y preventivas.
7. Aplicar medidas
Para cada falla debemos proponer una acción que elimine o reduzca el riesgo. Del mismo modo, cada acción debe tener uno o más responsables, una fecha límite de ejecución, materiales necesarios para cumplir el objetivo y una localización específica, entre otros elementos necesarios.
8. Seguimiento de las medidas aplicadas
Al igual que en toda matriz de evaluación de riesgos, necesitamos realizar las respectivas tareas de seguimiento e inspección, para determinar si las acciones implementadas fueron exitosas, o si debemos realizar ajustes (mediante correcciones puntuales o un nuevo proceso).
DataScope I El software ideal para digitalizar procesos
Identificar las diversas contingencias que perjudican la cadena productiva de una empresa es una tarea compleja que requiere del apoyo de herramientas digitales capaces de agilizar procesos.
En DataScope sabemos que la detección oportuna de estas posibles fallas es crucial para aplicar acciones correctivas a tiempo y evitar riesgos.
Por ello, con la plataforma digital de DataScope podrás, por ejemplo:
- Crear checklist digitales personalizadas y almacernarlas en la nube
- Asignar checklist de inspección a trabajadores específicos para que las completen desde la App
- Realizar un seguimiento en tiempo real de los formularios completados
- Integrar los datos recopilados con un ERP o otros sistemas de gestión utilizados
- Contar con métricas en tiempo real
- Trabajar sin conexión a internet
- Tener seguimiento GPS de las diferentes respuestas completadas