En los entornos productivos, SMED (Single-Minute Exchange of Die o cambio de herramienta en solo diez minutos) introduce la idea de que cualquier inicialización de un proceso no debería durar más de diez minutos.
Es por esto que los SMED nacen ante la necesidad de reducir el tamaño de los lotes que pasaban por las planchas de estampado. La aplicación del método SMED permitió no solo disminuir los tiempos, sino que también optimizar todo el proceso productivo. Por lo que actualmente se utiliza para las preparaciones de todo tipo de máquinas en diferentes rubros.
¿Para qué sirve SMED?
Al poder disminuir los tiempos que utilizamos en el cambio del proceso productivo de un determinado producto, los SMED pueden generar importantes ventajas competitivas al reducir el tamaño de los inventarios, maximizar la capacidad y flexibilidad productiva, y por supuesto, minimizar los tiempos de producción.
Con esto, podemos producir varios modelos en una misma línea de producción. Lo cual permite reducir costos y conseguir cambios de demanda más ágiles y flexibles.
El proceso SMED se divide en cuatro etapas:
1- Estudio de la operación de cambio: en esta etapa se busca evaluar los procesos o maquinarias para conocer sus funcionalidades y de esa forma, proyectar o desarrollar cambios.
2- Separar tareas internas y externas: en este punto se determinan los diferentes tipos de tareas, entendiendo como internas las operaciones que se deben realizar con la máquina detenida, mientras que las externas son aquellas que pueden realizarse mientras la máquina está funcionando. Esta etapa de diferenciación es fundamental para todos los procesos relacionados con el SMED.
3- Convertir las tareas internas en externas: es el punto más difícil de todo el proceso, ya que requiere un análisis profundo por parte del equipo de desarrollo, donde se busca determinar cuáles son las tareas que se pueden realizar antes de detener la máquina, o en paralelo, y si de esa forma reducirán directamente el tiempo de detención.
4- Perfeccionar el proceso de tareas: algunos cambios utilizados en este proceso pueden permitirnos disminuir el tiempo necesario para realizar un cambio de modelo, mejorar la capacidad de realizar más cambios de modelo, fabricando lotes más pequeños y planificando en consecuencia un plazo de entrega y un almacenamiento menores. Generalmente con la aplicación de esta metodología es posible reducir el stock y de esa forma, mejorar considerablemente los tiempos de espera.
El SMED sirve para reducir el tiempo de cambio y para aumentar la fiabilidad del proceso de cambio, y gracias a esto, es posible reducir el riesgo de defectos, fallos y averías.
Con esto, la reducción del tiempo de cambio de referencia puede aprovecharse de dos maneras:
– Para incrementar la Efectividad total de los Equipos (también conocido como OEE) y la Productividad. Con lo que además es posible mantener la frecuencia de cambio de las referencias como el tamaño de los lotes.
– Para reducir el stock en proceso: esto se consigue incrementando la frecuencia de cambio de las referencias y reduciendo el tamaño de los lotes.
¿Cómo funciona el SMED?
En 1969 Shigeo Shingo, considerado el padre del SMED, definió sus fundamentos al conseguir reducir el tiempo de cambio de una prensa de 1000 toneladas de cuatro horas a apenas tres minutos, de ahí nace el concepto de «menos de 10 minutos».
Si bien la definición de SMED habla de reducir los tiempos de preparación en menos de 10 minutos, debemos de esta conscientes que conseguir esto no siempre será posible, ya que para que todo este método funcione de manera correcta, es necesario coordinar diferentes procesos que puedan funcionar de manera armónica.
Es por esto, que la realización del SMED consta de siete pasos:
1. Preparación Previa
Esta etapa consta de dos partes:
Investigar
Durante esta etapa se busca obtener datos históricos de los tiempos de preparación. Para esto es necesario observar la preparación in situ, conocer el producto, la operación, las máquinas, la distribución en planta (layout), y las instrucciones de la preparación que se realiza en ese momento.
Crear un equipo
Para este punto es necesario construir un grupo de trabajo, una formación necesaria sobre los fundamentos del SMED y darle a su vez los medios necesarios para poder realizarlo.
Este equipo debe estar constituido por trabajadores con experiencia en la preparación, personas con capacidad para hacer modificaciones técnicas y además, miembros de la organización que puedan hacer modificaciones organizativas.
2. Analizar la actividad sobre la que se va a centrar el taller SMED
Durante esta etapa es necesario documentar (ojalá con grabaciones audiovisuales) en detalle todas las actividades que se realizan durante el proceso de cambio. Si varias personas participan de la actividad, todas deberán ser grabadas.
Tras esta documentación, el equipo del taller SMED usará las grabaciones para detallar todas las actividades de las que consta el proceso de cambio de referencia. Así se puede obtener el tiempo de ciclo estándar del proceso.
3. Separar lo interno de lo externo
En esta etapa es necesario que todos los miembros del equipo repasen todas actividades del proceso productivo para de esa forma identificar cuáles son internas y externas.
En este punto es necesario detallar a todos los miembros del equipo que las actividades externas son aquellas que se pueden realizar con la máquina en marcha y por tanto su tiempo de ejecución no afecta al tiempo de ciclo total del proceso.
4. Organizar actividades externas
Como las actividades externas pueden realizarse con la máquina en marcha, en esta etapa es necesario que el equipo haga un ejercicio de planificación para que todas las actividades externas estén preparadas en el momento de comenzar el proceso de cambio de referencia.
Con los resultados obtenidos por el equipo, se puede desarrollar un check-list para hacer más sencillo el proceso a futuro.
Entre las consideraciones que suelen recoger esta lista, se destaca:
¿Cuáles son las preparaciones que necesitan ser hechas con anticipación?, ¿qué herramientas y piezas necesitan estar a mano de los operarios que van a realizar los cambios?, ¿en qué lugares deben estar ubicadas las herramientas y piezas?, ¿están las herramientas y piezas en buenas condiciones?, ¿dónde deben colocarse los elementos después de desmontarse?, ¿Cómo serán transportadas las herramientas y piezas?, entre otras interrogantes que es necesario tener definidas.
5. Convertir lo interno en externo
Este proceso es fundamental, ya que es donde el equipo debe definir un plan de acción para conseguir la conversión de todas las actividades que se han decidido convertir en externas por parte del equipo. Además, para cada actividad se debe determinar que se va hacer, quién lo va hacer y sus plazos para tenerlo terminado.
6. Reducir los tiempos de actividades internas
En esta etapa, el equipo debe de plantear ideas para mejorar los tiempos de ejecución de las actividades internas, buscando por supuesto, reducirlas.
Una vez que se ha definido una idea de mejora, el equipo debe definir un plan de acción para implementar esa idea de mejora.
7. Realizar el seguimiento
Finalizado el taller SMED es necesario realizar el seguimiento para ver si el nuevo estándar definido se está cumpliendo o hay desviaciones, y en ese caso cómo pueden arreglarse o tomar acciones correctoras.
El seguimiento suele apoyarse en dos soportes:
– Registrar todas las incidencias que se han dado durante la semana.
– Registrar todos los tiempos de cambio que se dan durante la semana para luego, en una gráfica, representar los valores máximo, mínimo y medio de cada semana. La evolución de estos datos muestra todas las posibles desviaciones.
De acuerdo a todo lo que hemos revisado, el método SMED implica una excelente oportunidad para disminuir los tiempos y los costos en nuestros procesos productivos. Un sistema que si bien requiere una coordinación muy completa de diferentes unidades y equipos de trabajo, sus resultados constituyen grandes avances en la optimización de los procesos internos y la relación con nuestros clientes finales.
Los CMMS son una herramienta clave para el correcto plan de mantenimiento preventivo de una organización, pero, además, pueden ayudar en diversas operaciones gracias a sus ventajas y beneficios. Lo más importante es que nos permiten dejar de tener una posición reactiva y asumir una actitud mucho más proactiva a la hora de planificar el cuidado de nuestros equipos e instalaciones. Para de esa forma podamos aumentar la calidad de nuestro servicio que entregamos al cliente final.
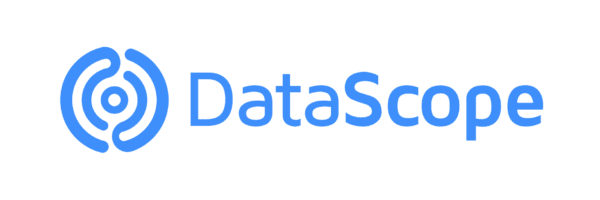
Digitaliza las Órdenes de Trabajo utilizando una App inteligente para las tareas de Instalación y mantenimiento.
DataScope es una plataforma de fácil implementación que digitaliza las Órdenes de Servicios de las empresas. Benefíciese de la transformación digital y reduzca los tiempos: obtenga equipos eficientes en terreno, mantenga todos sus datos centralizados y genere reportes completos.
Conozca más sobre nuestro servicio gratuito: